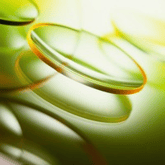
Uniform film thickness is essential for effective optical and medical coatings. If the film thickness on a medical device is not correct, the product will not interact properly with the body. If an optical film is too thin, its product efficacy is impaired; if too heavy, visual performance is frequently compromised. Viscosity is critical for maintaining desired film thickness. As the preferred viscometer supplier for many medical and optical coatings worldwide, Cambridge Viscosity has identified seven critical factors for optimal performance.
1) Achieving proper film thickness is critical for coating success. Incorrect film thickness results in unusable end products, varying from the distortion of optical characteristics to unacceptable in-vivo interactions. Incorrectly coated items are typically scrapped, along with the coatings themselves, which incurs costs such as the recovery costs for any volatile organic compounds evaporated in the process.
2) Viscosity is an excellent indicator of coating solids and film thickness. The concentration of coating molecules in the fluid directly impacts its resistance to flow. Viscosity is an excellent indicator of the amount of solids in the fluid and in the resulting film. An alternative to in-process monitoring is destructive testing, which results in scrap from the test and off-spec production between tests.
3) Control temperature for accurate viscosity measurements. Temperature significantly impacts viscosity. Temperature control typically includes insulation on the pipe sections, as well as water-jackets or heaters on the sensors plus the use of temperature-compensated viscosity to mathematically remove any minor temperature-variations.
4) Small sample viscometers are necessary. Fluid volumes in medical and optical coating systems are small. 4-5 liters of coating is typical for the entire fluid system including the reservoir, pump, dip tank and filter, as well as the associated tubing, and any required sample conditioning is simpler with smaller amounts of fluid.
5) Viscometers must be accurate in fluid viscosities of 200 cp or less. Medical and optical coating viscosity is typically in this range. Sensors must be accurate, repeatable and have excellent calibration stability in the 1-200cP range, despite utilizing very small amounts of fluid. Oscillating piston technology is far superior to torsional or vibrational sensors in these applications.
6) Incorporate viscometers that are easy to install and use. The viscometer is incorporated into the process system, not vice versa. It should be compact, utilizing materials that are compatible with the fluid being measured; self-cleaning and inherently low maintenance (no moving seals, linkages, or surfaces for evaporation). These viscometers must also have the necessary approvals for hazardous locations including ATEX and FM.
7) Utilize the same technology for in-line process and lab viscometers. This capability facilitates analysis of process results and simplifies trouble-shooting for any special condition that might occur.
Cambridge Viscosity is the leading supplier of viscometers for optical and medical coatings worldwide. They are inherently well suited to meet medical and optical requirements. Cambridge lab viscometers and process viscometers use the same core technology and are fully compliant with ASTM D7483. Cambridge instruments are compact, require small amounts of sample, incorporate temperature sensors and are extremely accurate, repeatable and robust. They incorporate the lessons learned and are fully proven as reliable devices for medical and optical coating control.
About Cambridge Viscosity
Cambridge Viscosity, the leader in small sample viscosity systems, provides automated viscometers used in coating, life science, oil and chemical applications to optimize product and process performance. Cambridge's global reach provides application engineering support and service wherever and whenever needed.