Monitoring the viscosity of coating products to achieve higher product quality and reduce maintenance downtime
CHALLENGE
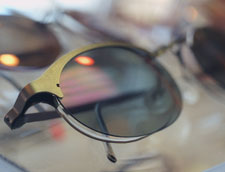
Controlling the viscosity of coating products is a significant challenge for manufacturers across a wide range of applications, from optical and medical to drum coating. The fluids are often difficult to work with and must be formulated and used within strict parameters to achieve the desired film weight, thickness, and image characteristics.
Incorrect film thickness can result in off-spec products that have to be reworked or scrapped, contributing to waste and unnecessary expense. Operational characteristics—such as temperature changes, blending variations in coating materials, and process-driven evaporation—make off-line measurements impractical.
A global manufacturer of laminating and coating solutions, needed a more efficient way to manage viscosity for their high-tech applications in solar, photovoltaic, safety, and security. Viscosity is an excellent method for managing coat weight, as it correlates tightly with the level of solids in a fluid. When they know their solids are correct, they know the wet coat will be correct, and, once cured, the dry coat will be correct. The company’s existing viscometers—based upon vibration technology—were routinely experiencing coating build-up, which threw the calibration off and required ongoing maintenance and repair.
SOLUTION
They replaced their existing viscometers with ViscoPro viscometers from Cambridge Viscosity by PAC. Based upon oscillating piston technology, the constant motion of the piston keeps the measurement sample fresh while mechanically scrubbing the measurement chamber. The patented self-cleaning design ensures continuous monitoring and operation without costly maintenance and frequent re-calibrations. The automated, in-line ViscoPro viscometers are integrated into the company’s programmable logic controller (PLC) so that they can easily retrieve data and track performance.
“In 10 years, we have never had to re-calibrate the Cambridge Viscosity viscometers. We are very pleased with the results and the consistency that we have been able to achieve with our coatings. The ability to more precisely monitor viscosity has allowed us to reduce waste by nearly 80%.”
— Senior Development Engineer
“As an engineer, it is great to install equipment that doesn’t have to be serviced every day. The ViscoPro viscometers are reliable and require almost no maintenance as they are self-cleaning. Although we rarely have to clean the viscometers, when we do, it takes us less than five minutes.”
— Control Systems Manager
RESULTS
The Cambridge Viscosity viscometers have enabled this manufacturer to produce better, more consistent products to their customers while saving money. Tighter control of their process allows them to use less coating while maintaining the highest quality and staying within spec. The viscometer’s compact design allows operators to quickly move viscometers to new work stations to meet the rapid changeover demands of production processes.
TEMPERATURE-COMPENSATED VISCOSITY
For many coating processes, viscosity is the primary measurement and process control variable that helps to determine the proper percent solids and consistent coating thickness. It is necessary to maintain a uniform film thickness throughout the manufacturing process. However, fluid viscosity is impacted by temperature variations that occur in the process, as temperatures in product environments are often not controlled. Temperature swings can cause the same solids content in a fluid to have differing viscosity values from day to night or season to season. Viscosity measurements need to be correct despite temperature variations. Temperature-compensated viscosity—the measurement of raw viscosity that is adjusted for temperature—is key to achieving coating consistency.
Temperature-compensated viscosity determines the viscosity of a fluid at a reference temperature that is different from the actual process temperature. TCV mathematically removes the variation in viscosity caused by temperature to determine if the change in viscosity is being altered by the percent solids present, the desired control parameter for most coating operations.
ViscoPro viscometers incorporate TCV calculation. TCV gives manufacturers confidence in the stability of its processes through greater process control. TCV is a valuable and useful viscosity control method for a wide range of coating applications.
FEATURES
- Easy to install
- Self cleaning, with very low maintenance requirements
- Small footprint
- Highly stable
- Accurate in low viscosity range