When it comes to rotating equipment, it’s a question of when—not if—a failure will occur. Engine breakdowns, for example, are often caused when the bearings in rotating parts fail. What does this have to do with viscosity, you may be wondering. Faulty bearings can generally be traced to one of three issues: 1) Severe service conditions, 2) improper handling or installation, or 3) poor lubrication.
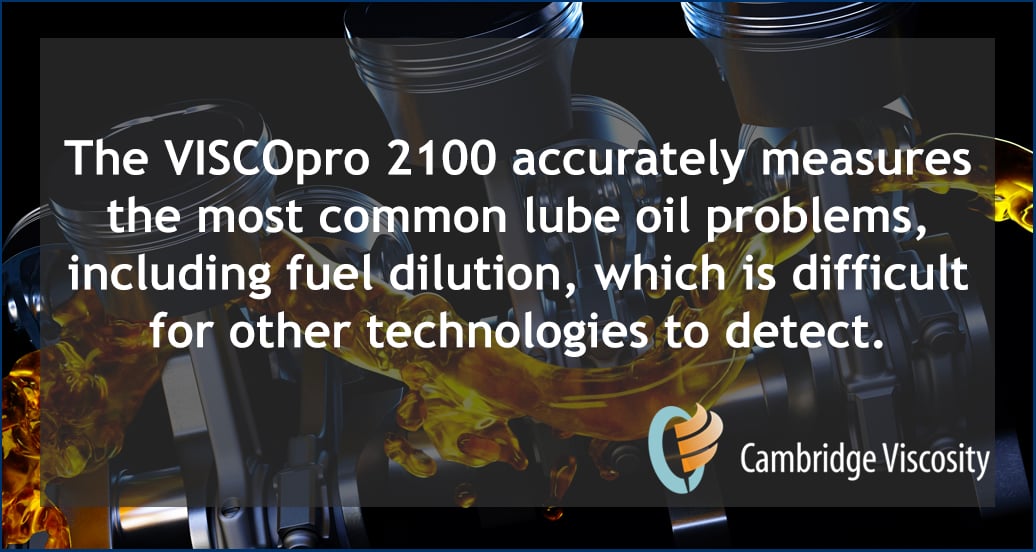
Improper lubrication, in fact, can be traced back as the root cause of the bearing failure about 50% of the time. This can occur when the lubricant’s lubricating properties are insufficient. Bearing failures can frequently be traced to viscosity breakdown as a result of fuel dilution, additive oxidation, soot, water, various other contaminants, or thermal degradation.
Cambridge Viscosity VISCOpro 2100 oil condition sensor (301), monitors the viscosity of the lubricating oil to prevent viscosity breakdown. Because viscosity is an indicator of oil health, real-time, dynamic viscosity measurements and trending can provide an early warning of oil and equipment failures.
By providing data that can be used for immediate intervention, the VISCOpro 2100 helps to prevent serious problems. Typically, maintenance personnel regularly send samples to off-site laboratories for analysis or change the oil on a scheduled basis. The VISCOpro 2100 reduces the amount of laboratory sampling that is necessary, and the continuous online monitoring allows operators to catch a problem with the lubricant before it becomes critical and leads to failure. Also, it allows operators to increase the interval between laboratory checks and lubricant changes.
The VISCOpro 2100 is particularly good at detecting fuel dilution, which is a critical parameter, and difficult to measure with any other technology. The VISCOpro is the only sensor available that can detect all the parameters of fuel problems, like fuel dilution, additive oxidation, soot, and water.
It is a rugged, accurate, and repeatable technology, even in environments with heavy vibration. The motion of the piston monitors the fluid viscosity and keeps the sensor’s measurement chamber free of debris, so the sensor doesn’t require operator intervention. It includes a temperature detector, allowing the capture of both temperature and viscosity in each measurement.
Results:
- Detect small changes in viscosity in real-time, even as low as .25% fuel dilution
- Avoid bearing damage in between lab analyses
- Incorporate temperature compensation to adjust for normal temperature effects on viscosity readings
- Expand lab testing intervals
- Extend periods between oil changes
- Best technology available for detecting fuel dilution