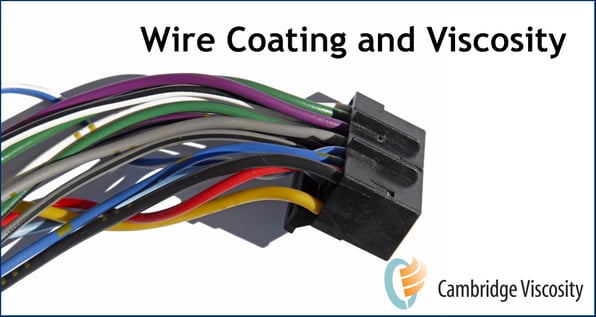
Wire is a component of nearly every manufactured product, from cars and computers, to generators, audio equipment, and watches. There are 80 feet of wire in a Slinky and 80,000 miles of wire in the Golden Gate Bridge. There are thousands of applications for wire. The global cable and wire market spans manufacturers of magnet wire, speaker wire, cable wire, integrated circuits, power transformers, electric motors and solenoids, and wire used in automobiles and electronics.
Wires can be as fine as a human hair (60 to 120 micrometers), thick enough to wrap into a bracelet (.4600 of an inch), or shaped into squares and rectangles for use in transformers. Regardless of how it is used, however, almost all wire must be coated with enamel, plastic, varnish, or a related substance. Too much coating, or too little, and wire will fail to meet specifications for manufacture or proper use.
Fine wire or magnet wire is particularly challenging. The enamel coating must be precisely controlled to achieve proper dielectric insulation so that electric motors, transformers, and other electrical devices operate properly in appliances, cars, and computers, to name only a few applications. Precise control of wire coatings is a critical job to ensure quality control and to meet customer requirements.
Why coat wire?
Wire is used in a variety of applications to enable electric current to pass from one component to the next. Controlling conduction — the ability of an electric charge to jump from one atom to another — is the primary reason wire is coated with a variety of substances, from varnishes to plastic, polymers, resins, and other non-conductive substances. Many wires are double-coated; coated wire is available in a variety of ‘build’ classes, ranging from single build to quadruple build. Build refers to the thickness of the coating, or insulation, which in turn corresponds to the ‘breakdown voltage’ rating, or the point at which the coating no longer prevents electric current from arcing. Coated wire is classified and sold by diameter, as measured in American Wire Gauge (AWG) or Standard Wire Gauge (SWG), in temperature class and insulation class.
Wire coating application
Applying the proper film thickness is the most important part of the coating operation. Uniform film thickness is a function of the concentration of coating solids in the fluid. Measuring the resistance to flow, viscosity correlates well with the molecular concentration. The wrong film thickness makes the end product unusable for the application for which it is targeted. Many coating problems are blending or evaporation-related, making off-line measurement impractical.
Most wire is coated using a dip-coating process. Wire is run through a coating bath and then through a metal wiping die, where excess coating is removed. Dies may be constructed with holes calibrated for different gauge wires, or they may have a set of grooves cut into the die in which the depth of the groove controls the amount of solution that coats the wire. Often, coatings are applied in several passes with visits to an oven in between coats to dry or cure the coating.
Most coatings have a number of process variables which must be monitored, e.g. temperature - both of the solution and ambient temperature; ambient humidity, and percentage of solids and solvents in the mixture. Variations in ambient temperature, for example, can evaporate solvents in the coating, increasing solvent costs and affecting coating thickness and drying times. Coating viscosity is a critical variable, one that can be challenging to measure and control.
Approaches to controlling wire coating viscosity
The most basic approach to managing wire coating viscosity is off-line testing. Coating is removed from the process and taken to a lab where viscosity is measured using a viscometer. A number of Cambridge Viscosity customers who used off-line testing have found the process inefficient, allowing potentially out-of-spec wire to pile up or require line shutdowns. Additionally, the measurement is inaccurate: ambient temperature changes between the vat and the lab inevitably affect viscosity readings. Viscosity measurement is very temperature dependent, often the lab is in a controlled environment.
Another approach to testing coating viscosity, the cup method, measures coating viscosity by placing a fixed volume of coating fluid in a cup and allowing it to drain through a hole, with a technician timing how long it takes for the fluid to drain. A longer drain time means higher viscosity. Many companies have discovered this method has a number of issues:
- It’s not a continuous measurement, and cannot be included in an automatic feedback control loop
- The cup method is dependent on the physical condition of the cup, which can become encrusted with dried coating
- It does not measure temperature, and thus the effects of temperature on viscosity are not measured
- The method varies with each technician, making it difficult to achieve consistency.
A more accurate, consistent and process-friendly approach to measuring coating viscosity involves installing an in-line viscometer. A wide range of viscometers are available commercially. One drawback: many lack temperature measurement and thus do not have the capability to perform temperature compensated viscosity (TCV) readings.

TCV is a mathematical representation of the viscosity a process fluid would possess if its temperature were at a user-selected reference point or set point. Without TCV-capable in-line viscometry it is necessary to set the solution vat control unit at percentages above and below the optimal set point. This requires constant monitoring and adjustment of the temperature of the coating solution, which can lead to over-shooting or under-shooting the ideal solution temperature.
TCV allows wire manufacturers to monitor viscosity without having to factor in temperature fluctuations. The VISCOpro 2100 automatically calculates temperature-compensated viscosity. As the viscometer adjusts for temperature changes automatically, manufacturers have one less variable to worry about in a highly variable process. By keeping this factor constant, the manufacturer can easily fine-tune their process such as changing the coating thickness or speed with which they pull the wire through the coating bath.